Abstract
This paper describes the application of vibro-replacement stone columns to improve a weak foundation and allow substantial savings in both the project schedule and the quantity of fill material. Recent expansion of the Kooragang Coal Terminal boosted the coal exporting capacity of the Port of Newcastle to 100 million tonnes per year. Port Waratah Coal Services appointed Bechtel Australia to manage the construction of a new Stacker Berm and Coal Pad, which commenced in November 2005 and was completed in March 2007.
The Kooragang Coal Terminal site is underlain by soft estuarine sediments, which are susceptible to settlement via consolidation and creep. The completed machinery berms and coal stockpiles apply surface loadings of up to 180 kPa. The foundation treatment included the installation of about 6000 stone columns by vibro-replacement through the soft sediments to a natural sand stratum.
The performance monitoring included a large scale load trial undertaken during construction. Monitoring of settlement was undertaken throughout construction and has continued post-construction. The completed Berm and Coal Pad have now been monitored for over one year in service and the results are consistent with predictions.
This paper discusses the design of the stone columns, the test pad design, numerical modelling to predict performance and the monitoring results for both the test pad and the completed facilities.
1. Introduction
The Port of Newcastle is the largest coal exporting port in the world. Port Waratah Coal Services (PWCS) operates two export coal terminals: Carrington and Kooragang Island. The Kooragang Coal Terminal (KCT) has been in service since 1984 and over the years a series of expansions has resulted in an export capacity of 100 million tonnes per year.
Kooragang Island separates the North and South Arms of the Hunter River and was formed by the reclamation of a number of smaller islands, channels and mudflats. The highly compressible soft soils lead to significant stability and foundation settlement issues for KCT structures associated with the coal stockpiles, stackers, reclaimers and coal conveying streams. Historically, foundation treatment for coal stockpile pads and machinery berms has comprised preloading, generally because of the availability of both sufficient time and large quantities of sand (from dredging of the river).
The most recent expansion “Project 3D” presented new challenges in that there were substantial operational benefits to be gained from a shorter construction period and there was limited sand available for use as preload material. As a result a number of different foundation treatment methods were investigated by PWCS and the principal contractor Bechtel Australia Pty Ltd. Following a rigorous review, including site visits, technical and safety risk analyses, vibro-replacement stone columns were selected as the most appropriate form of ground improvement for approximately 50% of the new machinery berm and coal pad. The other 50% was treated by conventional preloading.
Prior to award of the contract, Douglas Partners carried out preliminary design of the stone columns on behalf of PWCS using finite element methods. Keller Ground Engineering was awarded the design and construct contract to undertake detailed design and installation of the stone columns. The two design approaches are discussed in Section 3. The project included a large-scale load trial as part of the design verification process (Jones and Friedlaender, 2007). The location selected for the trial was typical of the poorer ground conditions present within the ground treatment contract area.

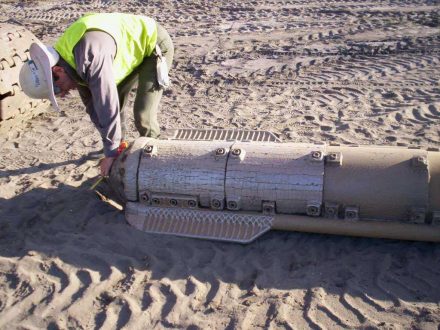
Figure 1: Installation of Stone Columns and Close-up of Vibro-Replacement Probe
2. Geotechnical Conditions
2.1 Subsurface Profile
KCT is underlain by a deep profile of estuarine sediments which includes layers of soft to firm silty clay. The principal geotechnical units, within the area treated by stone columns, are summarised in Table 1.
1 | Fill – Dredged Sand | Fine to medium grained sand with some silt, gravel, cobbles and slag inclusions,ranging in thickness from 0.6 m to 5.9 m |
2 | Alluvial Clay | Silty clay and clay, generally soft to firm, ranging in thickness from 1.6 m to4.5 m (average 3.3 m) |
3 | Sand | Fine to medium grained sand with some shell fragments, generally medium densethen becoming dense to very dense, to depths of 30 m to 35 m |
4 | Estuarine Sediments | Stiff to very stiff estuarine clay (4.1) and sandy clay/clayey sand (4.2) andunderlain by various layers of clayey sand, gravelly sand and further clay layers |
5 | Bedrock | Bedrock comprises siltstone and sandstone at depths of 50 m to 70 m, initiallyhighly weathered and very low strength, improving with depth. |
The typical soil properties of the compressible (clayey) strata at the site are outlined in Table 2.
Property (Unit) | Unit 2 Silty Clay / Clay | Unit 4.1 Estuarine Clay | Unit 4.2 Sandy Clay / ClayeySand |
---|---|---|---|
Unit weight (kN/m3) | 17 | 18 | 19 |
Plasticity Index IP (%) | 54 | 57 | 11 |
Initial Void Ratio e0 | 1.70 | 1.35 | 0.70 |
Undrained shear strength Su (kPa) | 15 | 100 | 150 |
Compression Index Cc | 0.90 | 0.67 | 0.16 |
Compression Ratio Cc/(1+e0) | 0.33 | 0.28 | 0.10 |
Recompression Ratio Cr/(1+e) | 0.036 | 0.027 | 0.008 |
Coefficient of Consolidation cv (m2/yr) | 3.5 | 5 | 50 |
Creep rate Ca(%) | 1.5 | 1.5 | 1.2 |
2.2 Settlement Estimates
Geotechnical analysis indicated that without ground treatment, neither the stability of the structures during construction and initial loading, nor the serviceability of the facility could be assured. Based on the performance of previously constructed phases of the coal terminal the client had identified the sensitivity of the plant to differential movements, and set strict performance criteria for the improved soils as outlined in Table 3.
Load (dead load / live load) | 95 kPa DL + 20 kPa LL | 180 kPa DL |
Total Settlement (after 17 yrs) | 200 mm | 350 mm |
Allowable Differential Settlement (after 17 yrs) | 0.3% transverse / 0.15% long | not applicable |
Allowable Diff Horizontal Displ. (after 17 yrs) | 0.075% | not applicable |
Estimated Total Settlement (after 17 yrs) | 300 – 860 mm | 430 – 1070mm |
The estimate settlements in Table 3 include settlement of the deeper clay layers and creep.
Without ground treatment there would be substantial settlements over time, as well as a high risk of shear failure upon initial application of the loads. Approximately 50% of the new stockyard had soft clays less than 2 m thick, and therefore could be preloaded within a reasonable timeframe. The remainder of the stockyard was treated with stone columns to reduce construction time and the need to import additional fill material.
3. Design Methods For Stone Columns
3.1 Preliminary Design
The preliminary design was undertaken to assess the efficacy of stone columns (and other soil reinforcement techniques) for the project, prior to going to tender for the ground improvement. The analysis was carried out using Phase2 finite element software. This enabled the stone columns to be explicitly modelled, rather than apply a composite modulus to the stiffened
soil-column material. The model included 1 m diameter columns on a 2.5 m square grid. The mesh arrangement is shown in Figure 2.
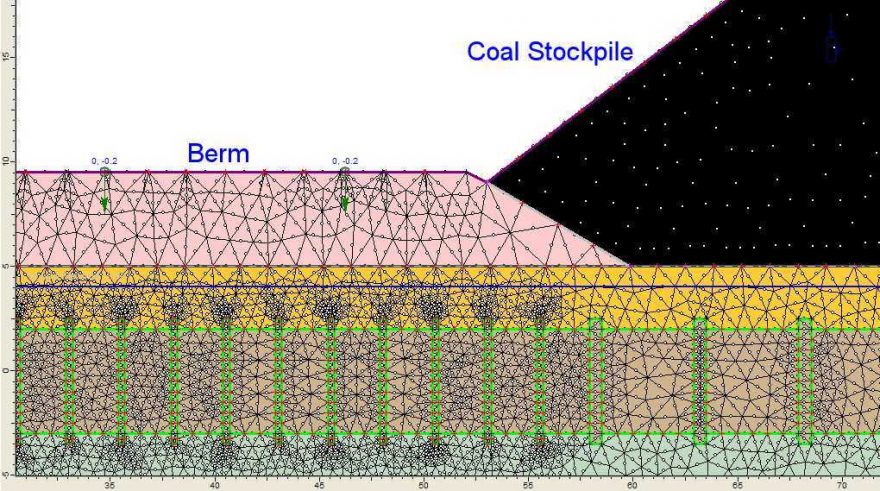
Figure 2: Phase2 Model for Preliminary Assessment of Stone Columns.
The stone column treatment would only reduce settlements within the uppers soft soils (Unit 2), and the assessment of overall performance also considered settlement of the deep estuarine clays (Unit 4) over the design period. The results of the preliminary design indicated the following settlements (Table 4) where stone columns are installed and the soft clay is 4 m thick.
Location | Estimated Settlements from Preliminary Analysis (mm) | |||
---|---|---|---|---|
Primary (Phase2) | Creep | Deep Clay Contribution | Total Settlement at 17 Yrs | |
Centre of Berm | 75 | 40 | 50 | 165 |
Centre of Coal Pad | 110 | 55 | 100 | 265 |
The preliminary analysis indicated that the use of stone columns would be feasible for the project, with estimated total settlements within the nominated criteria. Prior to construction, however, the contractor was required to carry out a more detailed design, including analysis of potential differential settlements.
3.2 Contractor’s Design Methods
The design of vibro-replacement stone columns is traditionally carried out using a partly analytical, partly empirical method developed by Priebe (1995). The contractor’s initial design was based on this method which applies an ‘improvement factor’ to the estimated settlement of untreated soil to determine the reduction in settlement (or improvement in performance). The improvement of the soil is based on the assumption that upon loading the column of granular material mobilises shear strength and the surrounding soil behaves elastically. The basic improvement factor n0 is given by the expression:

where ν = Poisson’s ratio of the soil, A = grid area, AC = column area, Kac = tan2(45 – фC/2), фC = friction angle of column material. The quantity AC/A is known as the area ratio.
Priebe also introduced adjustments to the improvement factor to account for the compressibility of the column material and overburden/material density effects. These result in modified improvement factors n1 and n2 respectively, with the latter being the final value used for design. For further information on these adjustments, the reader is referred to Priebe (1995).
The resulting design comprised 1.1 m diameter stone columns on a grid 2.75 m longitudinal spacing and 2.50 m to 2.75 m transverse spacing. The spacing is wider than that assumed for the preliminary analysis, and hence the settlements would be expected to be greater than the preliminary estimates shown in Table 4.
The prediction of differential settlements, and in particular transverse tilting of the berm, required more rigorous analysis. The contractor’s consultant carried out finite element modelling of the basic design, also using Phase2 finite element package, and a description of the design process can be found in Chan et al.(2007).
Location | Estimated Settlements from Preliminary Analysis (mm) | |||
---|---|---|---|---|
Primary (Priebe / Phase2) | Creep | Deep Clay Contribution | Total Settlement at 17 Yrs | |
Centre of Berm | 133 / 127 | 22 | 50 | 199 – 205 |
Centre of Coal Pad | 233 / 200 | 26 | 100 | 326 – 359 |
The above analyses indicated that settlements after 17 years would be close to the nominated criteria, which reflects the optimisation of the design to make full use of the available settlement tolerances. The tilting of the berm was predicted to be 0.11%, well below the criterion of 0.3%.
4 Stone Column Test Pad
4.1 General Description
A test pad was constructed to verify the design methods and parameters used in the design. The upper soft clays were 4.2 m thick at the trial pad site. A detailed description of the test pad set up and instruments can be found in Jones & Friedlaender (2007). The following presents a summary of the test pad arrangement and principal results.
The aim of the pad was to exert a foundation pressure similar to the berm and coal pad, as well as a gradation in pressure similar to the batter slope on the berm. A target pressure of 140 kPa was selected, considering the limitations of the site and available time-frame for construction. The test pad comprised a 5 m high fill embankment with the addition of sand-filled shipping containers to add further load.
Numerical modelling of the trial pad arrangement was carried out prior to construction to provide a prediction of the expected vertical and lateral deformations. Vertical settlement was predicted to be about 160 mm to 180 mm, while lateral displacements were estimated to be 20 mm to 30 mm, with the greatest deflection expected to be near the top of the clay layer beneath the toe of the trial pad batter slope.
4.2 Instrumentation
An array of geotechnical instrumentation was installed beneath and within the trial pad. These comprised six settlement plates, two hydrostatic profile gauges (HPG), eight inclinometers, three load cells and eight earth vector points around the perimeter of the trial pad. Two of the load cells were located directly over stone columns, while the third was located between columns. Four inclinometers were installed around the toe of the batter and four on top of the pad around the containers. Figure 3 shows the test pad site after installing the monitoring instruments and Figure 4 shows the completed test pad with sand-filled containers on top.
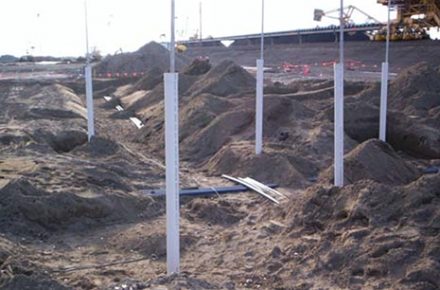
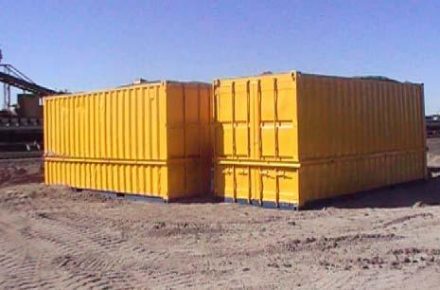
Five cone penetration tests were carried out prior to construction of the trial pad to provide specific data on the depth, thickness and strength of the silty clay layer underlying the pad.
4.3 Test Pad Monitoring Results
The principal results of the test pad monitoring are shown in Figures 5 to 7.
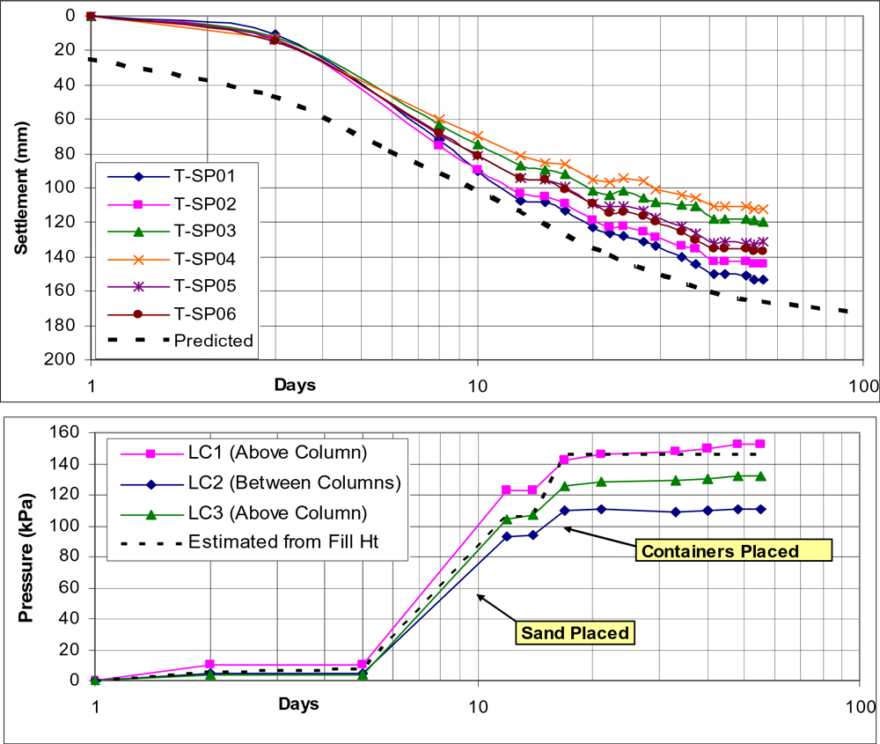
Figure 5: Settlement Plate Record and Load Cell Pressures from the Test Pad.
Primary consolidation was deemed to be substantially complete after about 40 days, which was consistent with expectations. The settlement plates recorded total vertical movements in the range 112 mm to 153 mm, slightly less than predictions.
The lateral deflections in the clay layer were up to 30 mm beneath the toe of the fill batter (see Figure 7) and up to 8 mm beneath edge of the containers, which were close to the numerical predictions.
The HPGs recorded 160 ±20 mm (see Figure 7) beneath the centre of the trial pad and exhibited a bowl-shaped deflection profile. The accuracy (repeatability) of the HPG’s was disappointing, being poorer than the manufacturer’s specification of ±10 mm. Nevertheless, the overall magnitude and deflected shape was consistent with expectations.
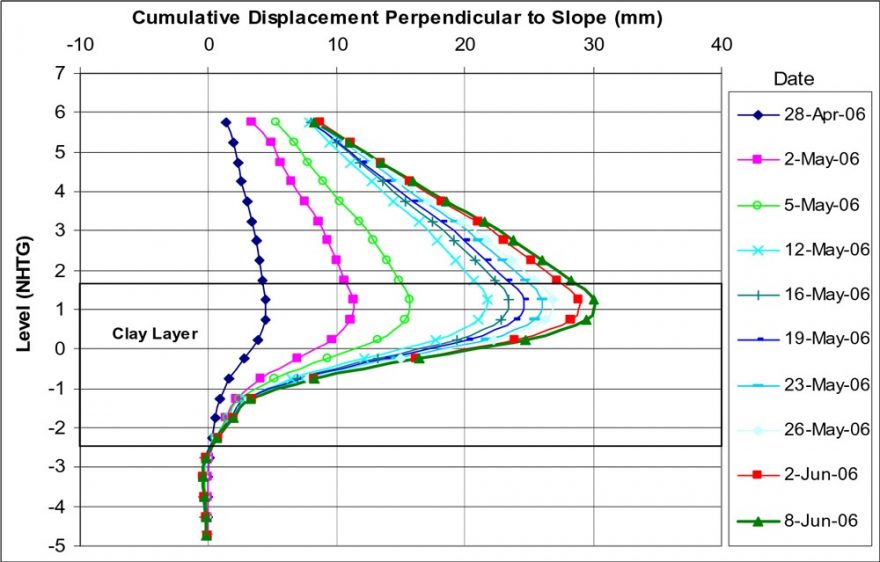
Figure 6: Plot of Inclinometer No 3 (toe of batter), which recorded the greatest lateral deformation
The five cone penetration tests (CPT) carried out before stone column installation were repeated after the trial (in between columns), and revealed an increase in clay shear strength in the range 50% to 100%. This is a result of consolidation of the clay, as the soil accepts a minor portion of the load, while the stone columns carry a major portion. The load cells implied that the columns attract up to 58% of the load, however the actual value is expected to be closer to 80%. Figure 8 shows the cone resistance plot from one of the before and after CPTs.
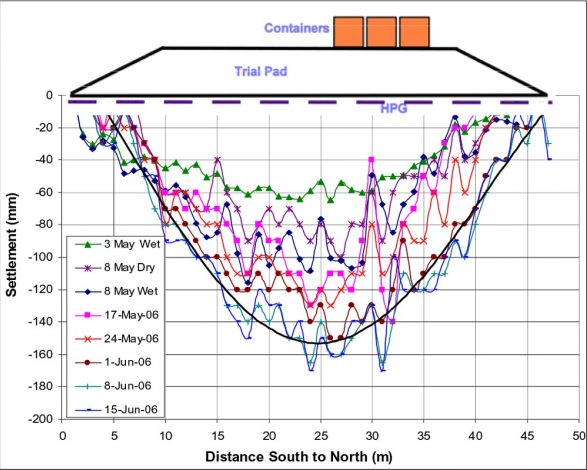
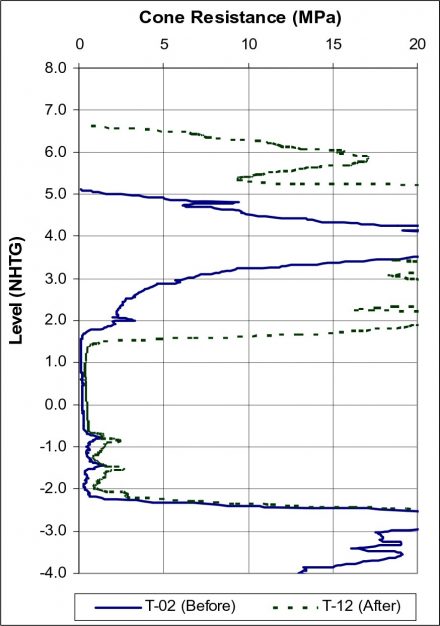
Figure 7 (left): Hydrostatic Profile Gauge (North-South)
Figure 8 (right): CPT before and after trial
The large-scale load trial provided a valuable test of the performance of stone columns under near full-scale load. The sand-filled containers were successful in adding further load to the foundation as intended. The trial confirmed predicted behaviour and successfully verified the methods and material properties adopted for the design of the vibro-replacement foundation treatment.
5. Post Construction Monitoring of Berm and Coal Pad
5.1 Machinery Berm
Two sets of rails were installed on top of the newly-constructed berm and these carry the Stacker which straddles the feed conveyor. Surveys of the rails have been carried out on several occasions since the rails were installed. The readings were taken at 15 m intervals along the rails. The HPG measurements provide additional backup to the survey data. This enables the total settlement to be determined at regular points along the berm, and differential settlement to be calculated in two orthogonal directions: across the berm (transverse tilt) and along the berm (longitudinal tilt).
A certain amount of settlement was expected to occur during berm construction, as the stone columns took up the load. Only the settlement occurring after completion of the berm and construction of the rails and conveyor is of concern. The post-construction settlement is driven by the additional loading of the Stacker, the adjacent loading of the coal pad (northern side only) and on-going creep due to the berm load. There was also an expectation that the stone column areas would settle more than the preloaded areas, and PWCS allowed for re-levelling of the rails during the first one to two years of operation.
Figure 9 shows the time-settlement trend for a section of the berm supported by stone columns in the area of thickest soft clay.

Figure 9: Settlement of Berm in Stone Column Area since Completion of Construction.
The envelope of the settlement trend on a log-time scale suggests that the total settlement (since completion of construction) will be within the criterion of 200 mm after the design period of 17 years has elapsed. It is noted, however, approximately 60 mm to 80 mm settlement occurred between topping out the berm and full completion of construction, which reduces the amount recorded as post-construction settlement. If the total settlement record is considered, the areas of thickest and softest clays have arguably settled a little more than predicted. This is mainly of academic interest, since the settlement of the rails rather than the whole berm is the prime operational consideration. If the observed log-linear trend represents secondary consolidation (creep), then the back-figured creep strain coefficients (Cαε) range from 0.6% to 1.5%. This includes an allowance for a small contribution to settlement from the deeper stiff clay layer (Unit 4), based on extensometer results from an earlier stage of the coal terminal development in 2000-2001 (Jones 2003).
The recorded differential settlement of the berm to January 2008 is illustrated in Figures 10 and 11. In regard to the transverse tilt (Figure 9), the coal stockpiles are situated to the north of the berm and a tilt in this direction is represented by a positive value, while a tilt to the south is negative. The negative tilt between Ch 1050 and Ch 1200 is due to re-levelling of the rails in 2007, and is expected to be compensated as the berm tilts further to the north due to coal loads. An examination of the time-settlement behaviour has confirmed a trend for tilting to increase to the north (i.e. trending positive).


Figure 10 (left): Transverse Tilt at 29 Jan 2008
Figure 11 (right): Longitudinal Tilt at 29 Jan 2008
5.2 Coal Pad
Prior to Project 3D there had been no settlement monitoring of the coal pads due to the practical difficulties associated with reading settlement targets within a coal stockpile area that has regular deposition and removal of coal. The installation of HPGs has allowed the settlement within the coal pad to be recorded. The first year’s record is shown in Figure 12 for selected HPG locations: two within the preloaded area and four within the stone column area.

Figure 12: Coal Pad Settlement Trends from HPG Readings.
Except for the preloaded section of the project, the coal pad did not have the benefit of being loaded during construction, as the berms were, and did not experience any load until the first coal stockpiles were placed. This meant that greater settlement was expected in the stone column areas compared to an equivalent preloaded area. The differential settlements were managed by alternate staging of the first five coal stockpile load cycles.
Although the HPGs are not as accurate as survey, the results indicate the settlement trends. The transitory loading of the coal pad is also evident by the variations in settlement, including evidence of rebound after coal removal. The results reinforce those obtained from the machinery berm, indicating that the preloaded area has experienced less settlement than the stone column area. The envelope of trends from the stone column area also indicates that the settlement after 17 years is likely to be within the criterion of 350 mm maximum settlement, with the upper end of the range being very close to the criterion.
6. Conclusions
The use of stone columns to reinforce the upper soft clay layers enabled a substantial savings in construction time and excess fill material compared to conventional preloading. The trade-off was increased post-construction settlements. The analysis and design process to control these settlements included traditional empirical methods and finite element analyses. The latter was particularly needed for prediction of differential settlements in both the longitudinal and transverse directions.
The numerical design process was complex and the design parameters and assumptions were verified by a large scale load trial. Post-construction monitoring has included survey of the berm rails and HPGs extending under both the berm and the coal pad. After one year of monitoring, the trends in both total and differential settlements indicate that the design criteria are expected to be met, with the areas of thickest soft clays expected to go close to the criteria after the design period of 17 years has elapsed.
7. Acknowledgements
The author wishes to thank the owners Port Waratah Coal Services for the permission to publish this paper, in particular Trevor Simmons for his valuable support. The following contributions are also acknowledged: Will Wright of Douglas Partners (test pad instrumentation), Grant Lindner of Bechtel (construction management), Rex Palmer of Daracon (earthworks including construction of the test pad), and Raj Deepak and Ernst Friedlaender of Keller (contractor’s design and project management, respectively).
8. References
- Chan K, Deepak R, Hoffmann G and Jones.P (2007). Designing stone columns to control horizontal and vertical displacements, Proc 10th Australia New Zealand Conference on Geomechanics, Brisbane, October 2007.
- Jones S and Friedlaender E (2007). Performance of an instrumented stone column load trial, Proc 10th Australia New Zealand Conference on Geomechanics, Brisbane, October 2007.
- Jones S R (2003), “Instrumented Preload at Kooragang Island”, Proc Mini Symposium on “Geotechnical Instrumentation & Construction Works Compliance Testing”, Sydney, 13 August 2003, Australian Geomechanics Society.
- Priebe H J (1995), “The Design of Vibro Replacement”, Ground Engineering, Technical Paper GT 07-13E.
Download the PDF here.
Jones-2008-The-Design-and-Performance-Stone-Columns-at-Kooragang